Digital Manufacturing
Inetum, a partner in 4.0 operations
Digital thread: Operational Stage

Supporting your industrial challenges
Today's industry players navigate in a complex and constantly changing environment.
Their long-term success depends on their ability to adapt quickly and innovate continuously.
Inetum helps manufacturers meet their operational challenges with solutions tailored to their specific needs:
Use tracking and tracing technologies to manage supply chain tensions, ensuring transparency and reliability of information throughout the chain.
Encouraging communication and collaboration through optimized data management and implementing digital tools - this helps improve coordination between the company's various departments and boosts profitability.
Deploy interoperability solutions to streamline data exchanges between IT and OT tools to improve coordination and operational efficiency between different management and production systems.
Inetum helps manufacturers protect themselves against cyber-attacks with solutions for: threat monitoring and detection, identity and access management, encryption, data backup and recovery.
Improving working conditions through new practices helps to attract and retain talent in industrial sectors.
Defining and deploying a robust, secure and scalable infrastructure for capturing, storing, managing and analyzing information is key to the transition to a data-driven model.
Understanding technological shifts is essential to staying competitive. Inetum supports manufacturers in the adoption of innovative technologies (IoT, AI, virtual/augmented reality, predictive maintenance, blockchain, etc). And in monitoring the evolution of traditional solutions (ERP, management and production systems).
Guide manufacturers in their choice of tools best suited to their production environment, regulatory context and needs. This enables to chart an evolutionary and sustainable technological course.
Getting to know your installations in order to improve their management and control. This reduces energy consumption costs, a key concern for manufacturers.
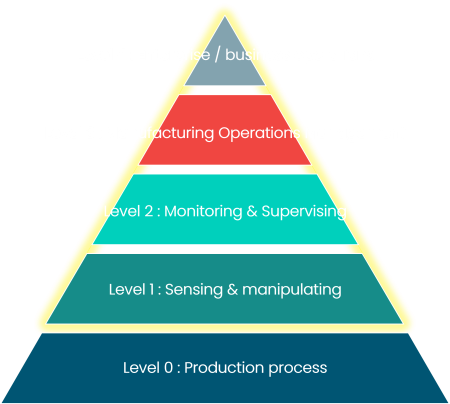
Our scope of intervention
We offer services through layers 1 to 4 of the ISA 95 Pyramid of Technology and Business Processes.
Supporting your operations 4.0
Inetum promotes digital solutions to optimize your operations of :
Support
Inetum holds a unique position in the Industry 4.0 market, providing manufacturers with dual expertise in consulting and integration services which improve the management of your resources, optimize your production processes and enhance the quality of your products.
We offer a complete and innovative integration package, taking advantage of all your data from your machines and your industrial information system. Our solutions are selected and customized to meet the specific challenges of your environment and use cases, such as:
- Monitoring and optimizing the OEE (overall efficiency ratio)
- Optimizing resources
- Quality management and continuous improvement
- Calculating the carbon footprint
- AI deployment
- Predictive maintenance
- Big data
To provide you with a global, real-time view of your operations, we rely on the integration of:
- Data platform
- IIoT Platform (Industrial Internet of Things)
- MES (Manufacturing Execution System)

Technology consulting, maturity audits, strategic framing, roadmap definition, project management, POC development, change management, etc.
Our consultants bring their expertise close to your business to help you build each stage of your success and support your transformation with an agile, collaborative and local approach.
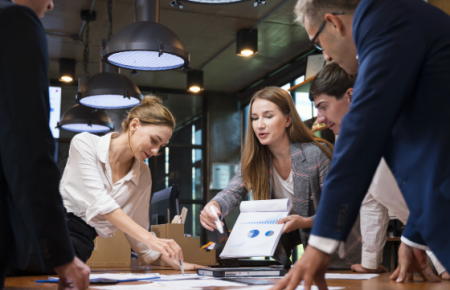
Our solutions
From data capture to logistics planning and management, we cover all your use cases, using the best solutions on the market, or developed in-house on open source bases:
- PTC (Discover more →)
- Siemens
- Cloudera
- Ignition
- Aveva
- Iconics
- CumuloCity Software
- Snowflake Datalake
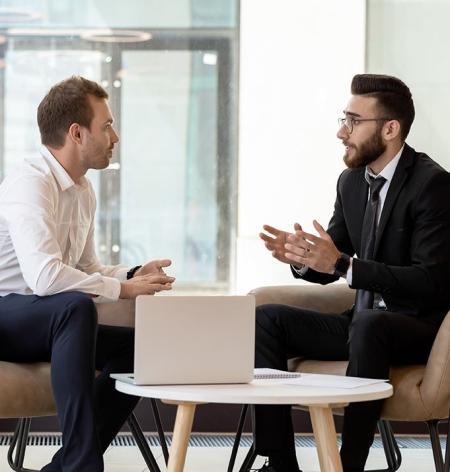