Predictive Maintenance
Predictive Maintenance : from ‘fail & fix’ to ‘prevent & predict’
In light of the major changes in the Energy and Utilities sector, ensuring the continuity of operations is essential in all circumstances. By identifying the risks of failure thanks to detailed knowledge of the equipment, predictive maintenance addresses this challenge. It promises an optimised production model.
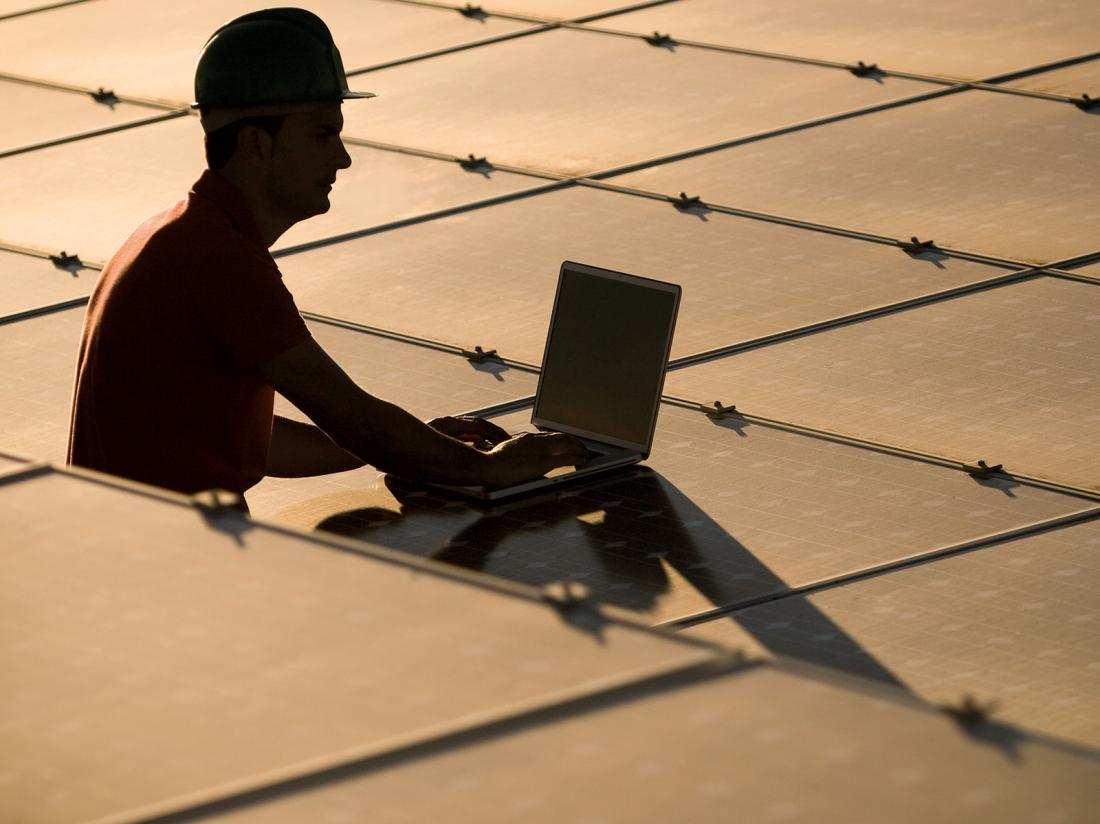
OVERVIEW
A sector facing major changes.
TAKING UP THE CHALLENGE
Predictive maintenance, a corporate programme.
REFERENCE POINT
USE CASE
In France, leaks account for, on average, 24% of treated and transported water, and up to 50% in some places (source: Observatory on public water and sanitation services*). To combat this loss, one network operator deployed acoustic sensors every 800 meters on its pipes. ‘Listening’ to the network makes it possible to detect new leaks and take appropriate action, thereby increasing efficiency.
(*Source : www.services.eaufrance.fr)
A wind farm operator installed vibration sensors to detect anomalies in mechanical components (gearboxes and generators) to prevent the risk of sudden failure and maintain its electricity production. A more detailed analysis resulting from the combination of these data with other factors (wind speed, temperature, etc.) makes it easier to make choices that increase the lifespan of the wind turbines.
Smart meters, such as Linky in France, provide a real-time view of energy consumption by area, right down to the electrical equipment in a residence. Beyond load balancing on its network, distributors can use this granular knowledge to offer consumption information and alert services should an electrical device fail. The result: reduced consumption and customer satisfaction and loyalty.